What is a CMMS Software System?
A Computerized Maintenance Management System, or CMMS for short, is a software program that helps organizations manage their maintenance operations. CMMS systems can vary in complexity, but all CMMS Software would typically provide a base line of certain features including an organizations ability to maintain an accurate accounting of all their assets (commonly referred to as the Install Base), track service history such as preventative and corrective maintenance work orders, and provide a basic service request ticketing system.
How is a CMMS Software used in a hospital environment?
A Computerized Maintenance Management System, or CMMS helps Hospital staff manage the all of their medical devices. This includes everything from smaller devices like blood pressure cuffs, infusion pumps, patient monitors, and surgical equipment, to "big iron" equipment like CT Scanners and MRI machines.
There are a number of reasons that a hospital cannot go without a CMMS software to assist their maintenance teams, biomedical departments, and imaging services teams. Computerize Maintenance Management Software helps with asset management, inventory management, work order management, work requests/service requests, scheduling and assigning tasks, business reports, real time data analytics, and much more...
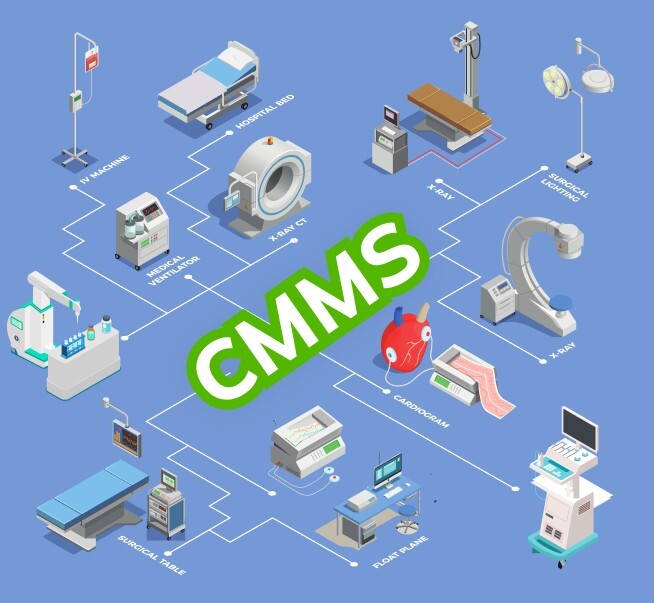
How big of a challenge is asset management within a hospital? How does having a CMMS Solution help?
Hospitals have thousands of medical device assets with a large variation in service requirements between different devices models; following preventative and corrective maintenance best practices would pose an insurmountable challenge for maintenance teams if not for the help of cmms software. To better understand the scope of these challenges let's consider: the different types of medical devices available, the estimated total volume of medical devices in use today, and how FDA requirements for medical-device-servicing makes a good CMMS solution a must have for any hospital.
How many medical devices are there?
According to the World Health Organization (WHO), there is an estimated 2 million different kinds of medical devices on the world market, categorized into more than 7,000 generic device groups.
How many assets are in a single hospital?
It's estimated that the average hospital in the United States has 10 to 15 medical devices per bed, so a 500 bed hospital could have 7,500 medical devices.
How many total medical devices are in all hospitals within the United States?
The American Hospital Association reported in 2022 that there are more than 920k Staffed Beds In All U.S. Hospitals. This means there is an estimated 10 to 15 million medical devices actively used in hospitals throughout the United States today.
How does Medical Device Risk Classifications impact service requirements?
Every device in a hospital must be serviced. However, they are not all serviced equally. The risk class assigned to a device will impact the frequency of service, and the mandatory tasks involved when performing certain service events. The Computerized Maintenance Management System (CMMS) helps ensure the appropriate service tasks are performed at the appropriate time for every asset in a hospital's install base.
The FDA categorizes all medical devices into one of three classes – Class I, II, or III. The FDA says they classify these devices "based on their risks and the regulatory controls necessary to provide a reasonable assurance of safety and effectiveness. Class I devices generally pose the lowest risk to the patient and/or user and Class III devices pose the highest risk."
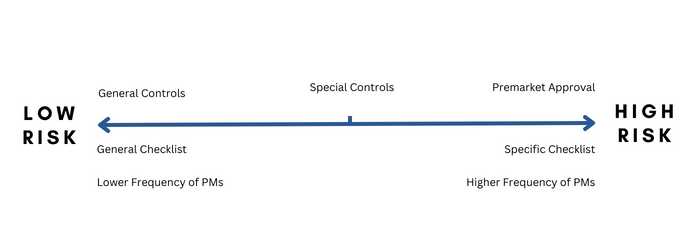
There are a number of quality requirements put into place by the FDA to regulate how medical devices are serviced. The risk classification assigned to a device directly relates to the service requirements for that device's maintenance plan. For example, medical devices with a higher risk classification will most likely require preventative maintenance service more frequently than medical devices with a lower risk classification.
In addition, medical devices with a high risk classification will also most likely require specific OEM preventative maintenance checklist items to be performed at the time of the Preventative Maintenance service event.
In contrast, medical devices with a lower risk classification may be able to follow a more generalized preventative maintenance checklist that was designed to cover all similar devices in a generic device group.
These are just a couple examples of the many nuances a hospital organization will face in managing their medical device assets. In addition to knowing which nuances applies to servicing each medical device, hospitals are also tasked with strict record keeping requirements.
What work order or service history data is required to be maintained?
Service reports are required to be documented and must include the following data:
- The name of the device serviced;
- Any unique device identifier (UDI) or universal product code (UPC), and any other device identification(s) and control number(s) used;
- The date of service;
- The individual(s) servicing the device;
- The service performed; and
- The test and inspection data.
In addition to these record keeping requirements, hospitals must also demonstrate that they have procedures in place to ensure best practices are followed for the maintenance of all of their assets.
If you were to attempt a paper process to manage all of these nuanced details for even a single device it would prove challenging. When you scale the challenge to thousands of different devices, many with unique service requirement variations, the benefits of equipping your maintenance team with CMMS Software quickly becomes clear.
Benefits of Computerized Maintenance Management
Process Standardization & Lowering Audit Risk
Many CMMS Software providers offer a variety of rich features to support the standardization of a hospital's maintenance processes. Through utilizing required fields, validation rules, record visibility controls, permission/access control features, workflow rules, etc... maintenance software helps hospitals demonstrate their ability to maintain controlled procedures around the maintenance of their assets.
When an off-the-shelf maintenance software can be customized to mirror the hospital's written procedures for work order/asset management, this provides an insane level of benefits to the hospital organization; Not only does this streamline the maintenance team's overall process of asset management, but it helps provide much needed solutions for quality and compliance.
The role of a well designed CMMS in a Joint Commission or internal audit is critical, as it can help Hospital staff prove that they are taking the necessary steps to maintain safety and compliance within their facility.
CMMS Reports & Data Analytics
Ad hoc Reporting
Many Computerized Maintenance Management Systems offer robust reporting so that maintenance teams have the ability to create reports, and analyze data in order to support various business needs. A good CMMS can provide the ability to quickly create ad hoc reporting to analyze asset data in real time.
Schedule Reports
The best CMMS Software offerings include highly desired reporting features such as Scheduling Reports, which can help maintenance managers save time and may also be an option for supporting routine meetings such as an Environment of Care Committee review meeting.
Relational Data Saves Time and Promotes Analytics & Reporting Capabilities
Hospital staff (both Maintenance Teams and Business Users) can use a CMMS Software to generate a number of valuable reports that can be used to identify trends and improve the overall efficiency of hospital operations, and gain real time insights for things such as:
- Medical Equipment Performance
- Preventative Maintenance Work Orders Compliance
- System Downtime
- Work Order Response Time
- Track Inventory Levels
- Analyze Labor Expenses
- Better understand Part Costs & Parts Utilization
- Compliance KPI Tracking
- and more...
Data Redundancy
CMMS Software can be cloud based and on premise. Either way, there are typically options to create and maintain backups of the hospital's maintenance data.
Enable Mobile Maintenance Processes for Users
Many CMMS Software providers offer mobile features. You can equip your support services teams with mobile maintenance capabilities through apps or interfaces designed for a technician's mobile device. These features will vary based on your CMMS provider.
Customizable Features
Many software vendors offer software advice and customization features that allow the CMMS Software to be flexible for a specific hospital's equipment management process.
Preventative Maintenance Work Order Automation
The FDA set strict guidelines for the frequency in which preventative maintenance service must be performed on medical devices. A CMMS system is used in hospitals to track and schedule preventive maintenance tasks for medical equipment. By tracking these tasks, hospital staff can ensure that all medical equipment is properly maintained and serviced regularly. This helps to prevent costly repairs, prolongs the life of medical devices, and ensures compliance with regulatory preventative maintenance standards.
Corrective Maintenance Work Order Management
When a piece of medical equipment breaks down, it is important to have a system in place to track and schedule the repair or replacement of that equipment. A CMMS system helps hospital staff to keep track of all corrective maintenance work orders and ensure that tasks are completed in a timely manner.
Work Load Balancing for Maintenance Teams
Corrective Maintenance Task Assignments
Obviously, a CMMS Software can assist with practical needs such balancing out the workload between team members performing Corrective Maintenance Work Orders. Through Service Requests and Work Order task assignments, you can monitor the volume of work being performed by each maintenance team member and reallocate work when necessary.
Preventive Maintenance Planning & Work Load Balancing
A well established CMMS Software can assist Maintenance Managers in planning ahead for the labor required over the course of a year for performing Preventative Maintenance Work Orders. This is commonly referred to as "PM Balancing", and can be a powerful solution for effectively managing the workload required to keep the hospital going, while also ensuring employee satisfaction, and reducing overtime.
As an example, knowing that your biomedical staff will take more vacation time in the Summer months and the Holiday season, you can plan ahead by ensuring that the heaver months for your hospitals PM Work Load does not overlap with peak vacation seasons.
Ticketing/Service Requests Process
Most CMMS Software's have some form of ticketing system to allow hospital employees to create a requests for service when a piece of equipment malfunctions.
Service Requests & Work Order Assignment
Many CMMS Software's have rule based ticket routing features to ensure Service Requests for Corrective Maintenance is routed to the correct maintenance team member.
Tracking Expenses in your Computerized Maintenance Management System (CMMS Software)
A CMMS system is helpful to track expenses related to a work order such as replacement part costs, a technician's labor, or even the cost to outsource the service related work to an OEM or third party provider.
What types of API integrations are common with CMMS Software?
There are a number of systems that hospitals may choose to integrate with the CMMS software. Some of the most common API integrations for CMMS software include:
- Recall Management Software
- Financial Systems
- Hospital Asset Tracking Systems (RTLS)
- Procurement Software
- Cyber Security Software
For a more detailed explanation of common CMMS integrations check out our CMMS integrations service: Integrate Your Hospital CMMS Into All Your Key Software Systems.
How to Organize Work Orders
How you organize your Work Orders will be based partly on the data architecture of your selected CMMS, and partly on the reporting, views and work order management preferences.
Data Architecture Design and Data Management
The exact way the data is structured will to a large degree depend upon which CMMS Software you choose to implement. Most all Hospital CMMS software solutions (both Cloud Based & On Premise) track similar data elements. Below is an example of what a Hospital CMMS Data Structure may look like.
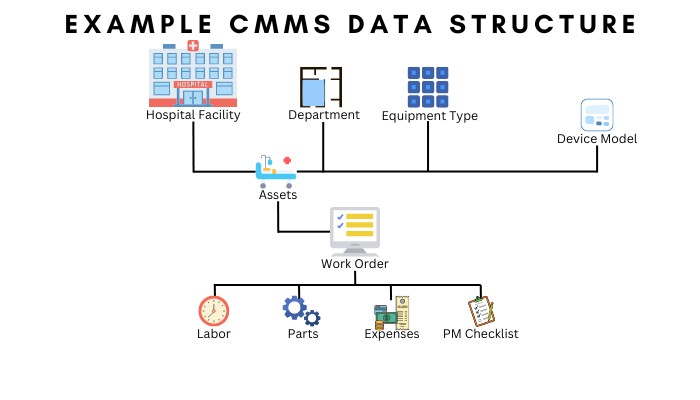
Generally speaking, most all CMMS Software will provide the ability to track various data in a relationship based data structure including:
- Hospital Facilities
- Departments
- Device/Asset Types
- Device Models
- Assets/Devices
- Work Orders
- Labor Tracking
- Parts Tracking
Organize How You See Work Order Data
There are a few different ways that you can organize how you view and manage the work orders in your hospital's CMMS.
A common work order management best practice is to set up multiple views to organize visibility of your work orders in different ways. This allows you to quickly access real time visibility to open work orders in a variety of ways so that you can quickly answer different business questions as they arise. This also allows you to see potential business challenges, or help you see when a work order may fall through the cracks.
Here are some common grouping methods used when organizing visibility to your open work orders:
- Equipment Type - easily see all open work order activities by the Device Type or Equipment Segment
- Department - quickly see the how many work orders are open by department. This can come in handy for a number of reasons. Whether answering an inquiry by a department leader who is asking about a Corrective Maintenance Work Order, or organizing Preventive Maintenance Work Orders by area of the hospital to prevent your staff from wasting time by being forced walk long distance with the hospital campus from one PM Work Order to the next.
- Location - similar to the benefits of viewing you data based on the Department, you may also choose to have views based on additional location identifiers such as Building, Floor, or Room. The options you have may vary based on your CMMS Software and how many location identifiers you keep track of on your Device/Asset Records.
- Maintenance Team / Team Member - by being able to see the volume of work performed by each team or team member you can: help ensure that work is balanced appropriately, manage employee performance issues, prevent unnecessary overtime, and more...
- Work Order Status - quickly view work orders by current open status to determine next actions needed by the maintenance team. You may choose to take this one step further with having one view set up for work order status on all open Preventative Maintenance Work Orders, and another view set up to see all open Corrective Maintenance Work Orders by status. This can be helpful to ensure that Preventative Maintenance Work Orders are completed within their compliant window of time, and Corrective Maintenance Work Orders are not aging. If may also help you know if you need to follow up with third party vendors for outsourced service; or if the work order status indicates it's pending parts delivery and a follow up to the parts provider may be required.
- Work Order Aging - Ensure that PM Work Orders are completed within their compliance window, and that internal KPI targets for CM Work Order completion is met.
Software Advice For Organizing Your Work Orders
By organizing your work orders, you can ensure that the most important tasks are completed first and that your maintenance team is working efficiently. You may need to seek software advice from your CMMS Software Provider to learn how to best implement these various work order organization strategies within your CMMS System.
Conclusion
If you have read this far, then you probably already know the important role that a good Computerized Maintenance Management System plays in the maintenance of medical devices within a hospital. Running a successful maintenance program within a hospital is no small task!
Ensuring quality of patient care is the highest priority, and it is a goal that simply cannot be achieved without a proper medical equipment maintenance program in place.
Since Covid hospital systems have changed, and most find themselves under immense pressure. By implementing and optimizing a CMMS Software within the hospital you can see many benefits including:
- Standardizing & optimizing your processes to prevent equipment downtime, ensure good maintenance documentation, and reduce audit risk.
- Improve analytics & reporting capabilities to provide real world business value to further optimize hospital operations.
- Improve employee satisfaction.
- Eliminate waste, and increase efficiencies.
- Reduce overall cost of service program and improve financial outlook for hospital organization.
Consider The Best Integration Options To Further Streamline Your Work Order Management Processes
Consider how integrating your CMMS Software can Improve Compliance, Increase Data Quality & Eliminate Duplicate Workflow Processes In Your Hospital.
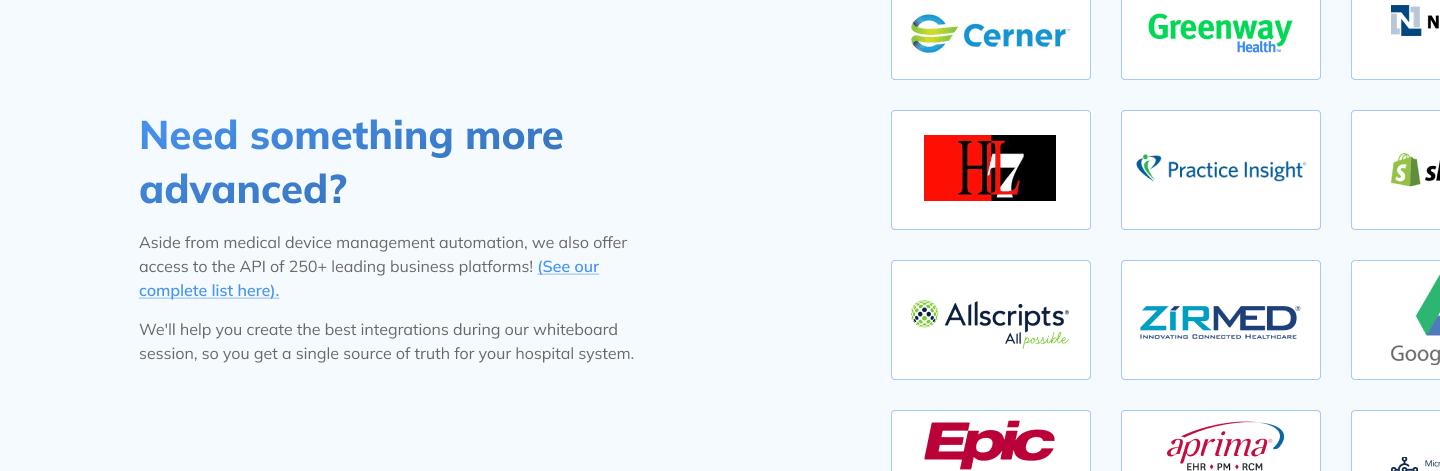
Explore all available integration
Autymate Can Help Optimize CMMS Software Processes Through Custom Integrations
See common user stories for CMMS Software Integrations including:
- CMMS Integration to Recalls & Alert Systems
- CMMS Integration to Remote Tracking Location Services (RTLS)
- CMMS Integration to Cyber Security Connection
- CMMS Integration to Financial System Connection
- CMMS Integration to Parts Procurement Services
- CMMS Integration to Financial System Connection
Why Work With Autymate Health
You need an integration expert who also understands the struggles you face in managing your hospitals operations. There's no need to expand or overload your own IT team who may be lacking the resources to deliver your projects in a timely manner, and who may not currently have a full understanding of the business problems you are trying to solve.
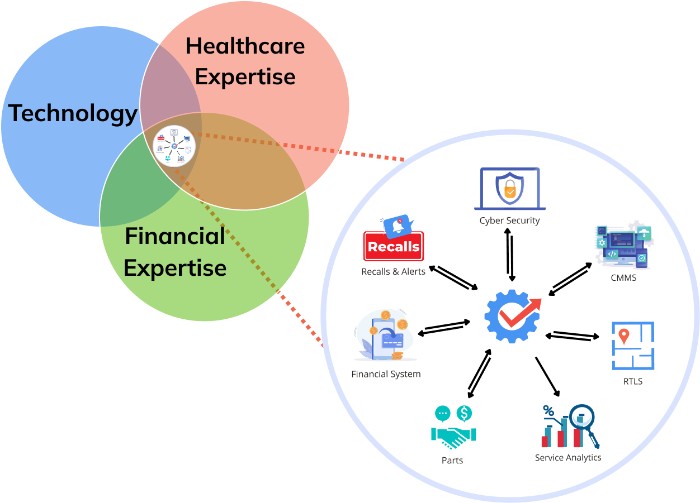
By doing what you do every day to manage your medical device service programs, you are enabling your hospital (or healthcare system) to meet it’s commitment to quality of patient care, and optimize patient flow to improve the patient's overall experience while they are in your facilities. What you do matters!! Turbocharge your projects by working with a partner who understands the technical, operational, and regulatory challenges faced by you and your organization.
Autymate Health is well versed in CMMS Best Practices and specializes in helping you connect your CMMS to various software to better support your Medical Device Service Program.